Avangard Holding is proud to rely on over two decades of experience and advanced academic education from prestigious universities both inside and outside the country. With the production of over ten thousand parts, including components for machinery, automotive, mold-making, oil and gas, petrochemicals, power plants, cement, and mineral processing industries, using alloys such as carbon steels, low-alloy steels, heat-resistant steels (stainless and refractory), manganese steels (Hadfield), high-chromium steels, and high-chromium cast irons, we are capable of producing parts based on specific analyses, standards, and desired characteristics. We are honored to serve esteemed industrialists by offering the best quality and most competitive prices, providing our casting services to you.
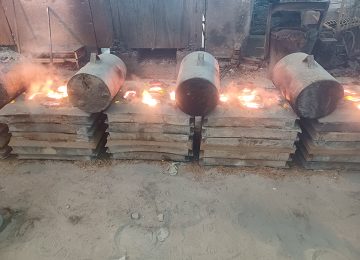
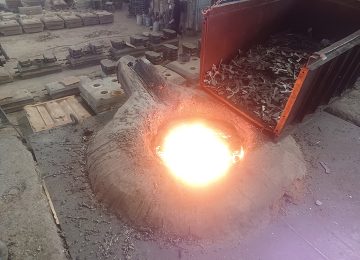
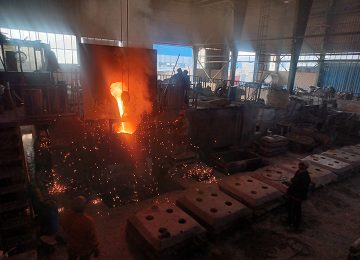
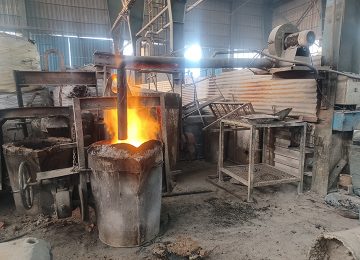
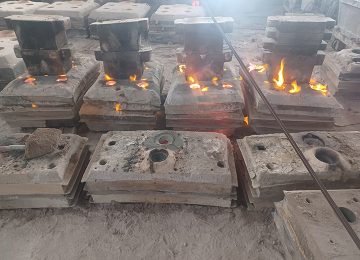
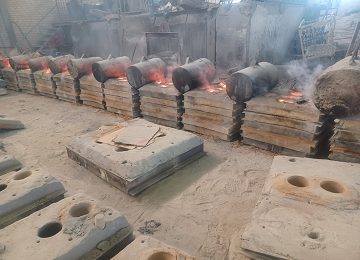
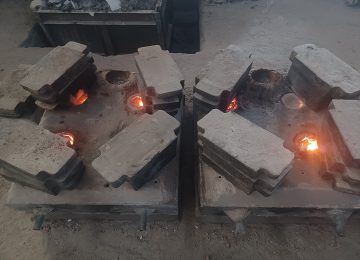
Casting has a history of 7,000 years. The oldest casting piece in the world is a copper frog dating back to 3200 BC, which was found in Mesopotamia. There are various methods for producing metal parts made of iron, steel, and non-ferrous metals (bronze, aluminum, brass, etc.). The most important method is casting. Casting is a mechanism in which metals and alloys are poured into a mold in their molten state, and after cooling and complete solidification, they take on the shape of the mold. The casting process is performed to shape the molten metal and produce complex parts.
As mentioned, casting involves shaping an alloy through melting and solidification. This simple yet practical method is the foundation of large steel industries worldwide. Although there are other methods for shaping various types of steel and cast iron, casting has many advantages over other methods.
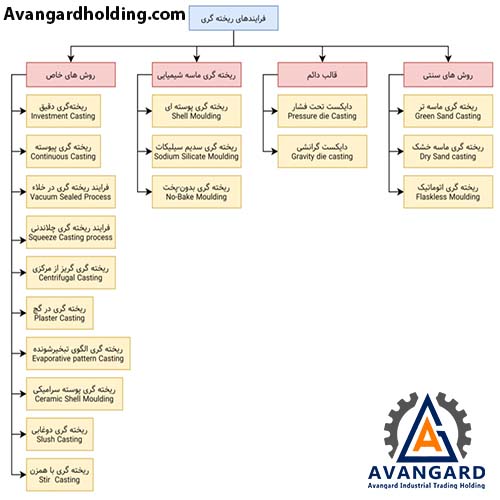
The metal casting industry is an important production mechanism that produces various casting products for human life. With the development of the global economy, the metal casting industry has been growing rapidly in recent years. The production capacity of cast metals worldwide has increased from 92 million tons in 2010 to 112 million tons in 2016. The metal casting industry produces parts with complex shapes that are used in numerous consumer and industrial goods.
Avangard Company, with its experienced engineering team and extensive expertise in producing various steel and cast iron parts, is capable of manufacturing parts with complex geometric shapes and alloys tailored to your requests. Later, we will discuss more about the alloys produced in melting and casting operations.
Related topic: “Cutting and cleaning in casting”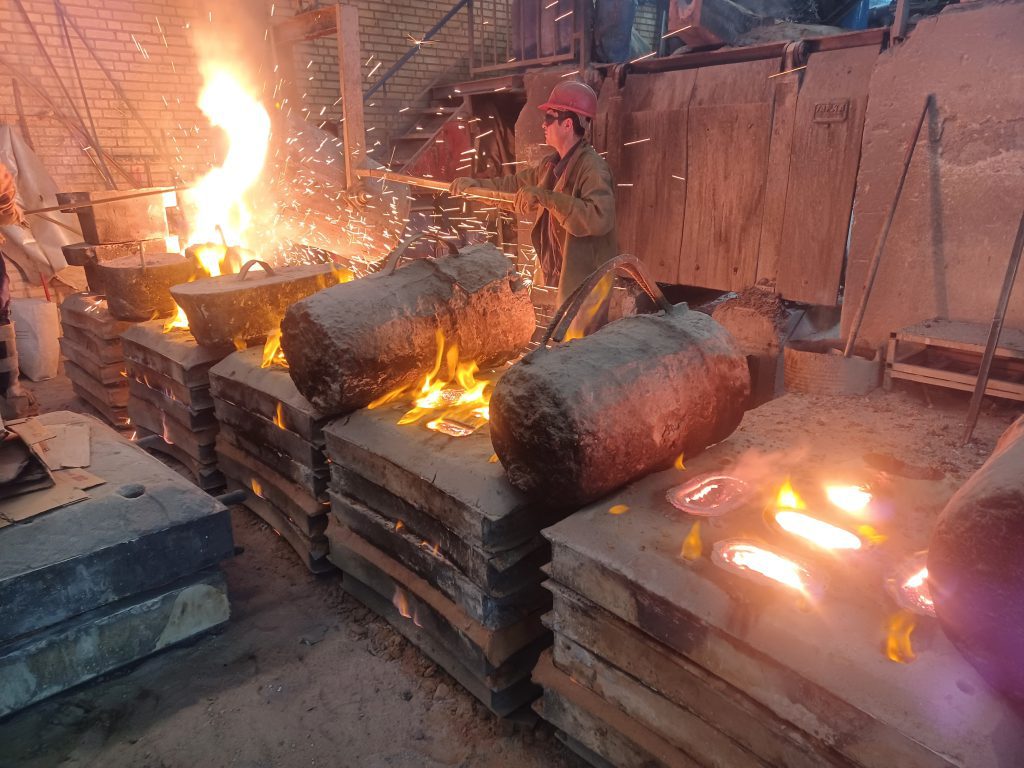
After the stages of molding and assembly, which we briefly discussed in previous sections on the Avangard Holding website, we now enter the melting and pouring stage.
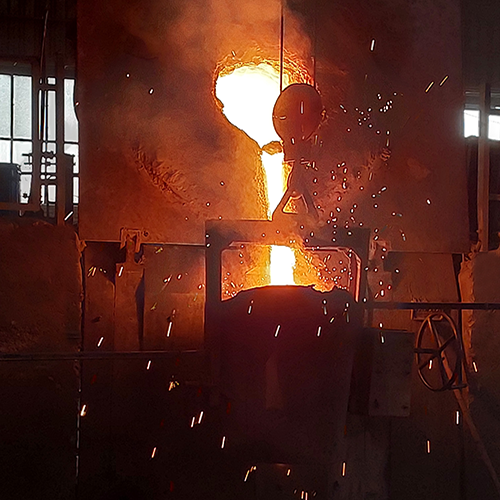
For the production of many metal parts, the manufacturing mechanism begins with melting the metals. In this case, it is necessary to raise the temperature of the metal to its melting point, and for metallurgical operations, it is often required to maintain it at the desired temperature. The use of an induction furnace is one of the best methods for carrying out this process. After precise alloying, the furnace operator, based on the calculated charge, performs the melting operation inside the furnace. Once the melt is prepared, a sample is taken for melt analysis using a quantometer and sent to the laboratory unit.
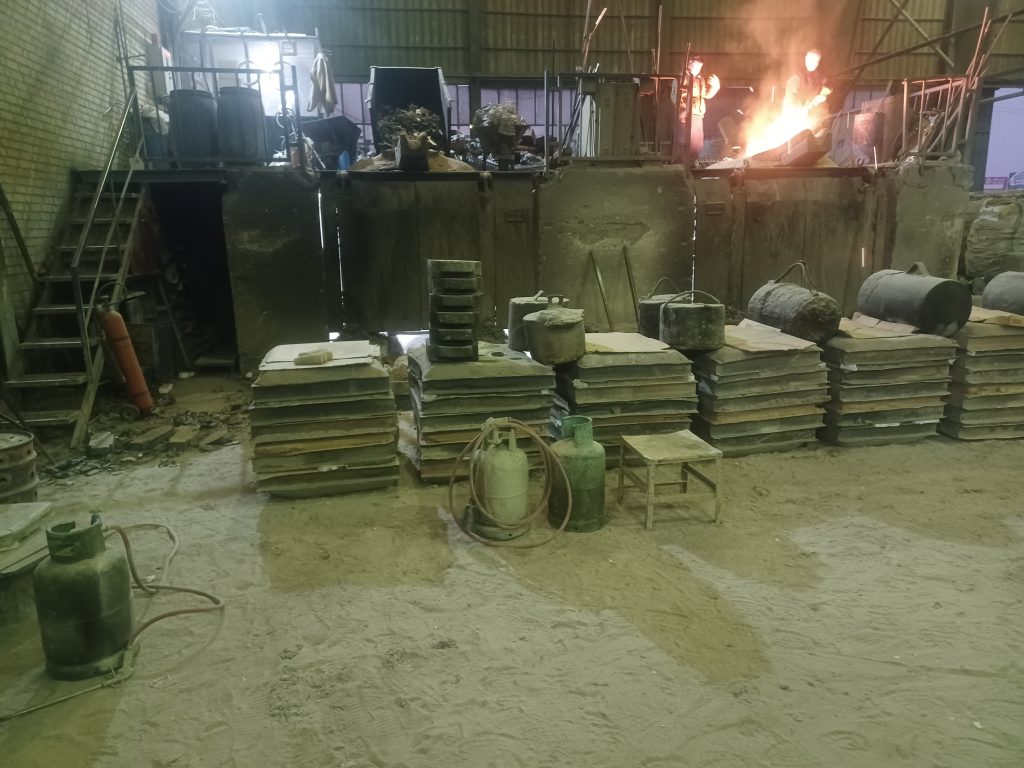
The measurement of various elements in the melt and precise control of the chemical analysis using a quantometer is carried out by experienced engineers in the Avangard Holding laboratory. This is done by first grinding the surface of the sample until it is completely smooth and free of any contamination or grease. The sample is then placed on the sparking area of the device from the polished section. The mechanism of this test is based on optical emission. The particles of the metal in question are decomposed into atoms and ions due to the spark, and these ions are excited and emit radiation. This emitted light is passed through an optical spectrometer via an optical fiber. Then, based on the wavelength range of the emitted light for each element, the most accurate emission line is selected to measure the concentration of that element in the sample. The emission intensity for each element is proportional to the concentration of the desired element in the sample, and using existing standard samples and calibration curves, the percentage of elements in the sample can be directly calculated.
After the spark, which is essentially the spark created by the device’s electrode on the surface of the sample, the experienced staff of the Avangard laboratory determines the amount of elements present in the sample using the wavelengths predefined for the device. Once the alloy is confirmed, permission to pour the melt into the mold is issued by the laboratory unit.
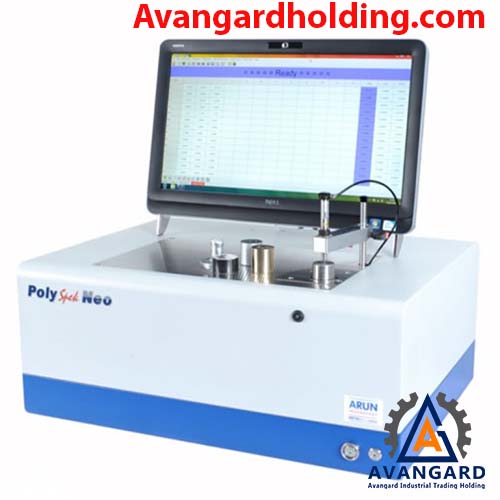
Why do we need a quantometer?
In the manufacturing of parts, determining the material is always one of the important factors for the performance of the part. The material of each part must be suitable for the working conditions, such as the working environment, operating temperature, working atmosphere, the material of other interacting parts, and the function expected from the part. Therefore, selecting the correct material and ensuring its analysis is crucial. To achieve this goal, the use of precise quantometers with an accuracy of hundredths of a percent is essential.
Related topic: “Laboratory and quality control in casting”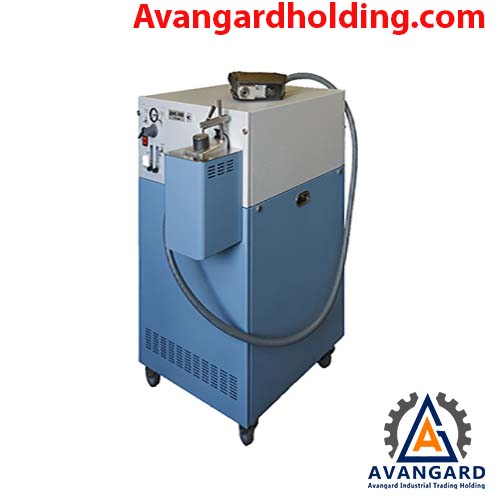
Some of the widely used alloys in the Avangard collection
The term “carbon steels” refers to plain carbon steels that do not contain significant amounts of alloying elements. These steels are primarily used in general engineering, construction, and hydraulic pressure equipment. Low-alloy steels, due to the presence of alloying elements such as chromium, molybdenum, and nickel, have higher mechanical properties compared to plain carbon steels. In carbon steels, the presence of suitable alloying elements in the composition improves wear and corrosion resistance.
Due to their excellent toughness and wear resistance properties, high-chromium steels are primarily used in material crushing processes. Considering their application conditions, this group of martensitic steels, offering wear resistance combined with excellent strength, has managed to position itself between the properties of manganese steels and high-chromium cast irons. Today, high-chromium cast irons are considered as an alternative to high-chromium steels in conditions where parts are subjected to moderate impacts and severe wear. This category of white cast irons has very good wear resistance, which is due to the presence of a martensitic matrix along with precipitated carbides. In conditions where the part is subjected to moderate impacts and severe wear, nickel-chromium cast irons are a suitable choice.
Heat-resistant steels are widely used for operation under high-temperature conditions. The type of environment and mechanical strength at high temperatures are the main criteria for selecting heat-resistant steel. Heat-resistant steels exhibit good corrosion resistance and mechanical strength over long operational cycles. Steels composed of iron, chromium, and nickel primarily have an austenitic matrix and demonstrate good strength and toughness at high temperatures. Additionally, nickel-chromium alloys, in conditions where the part is exposed to ash from the combustion of heavy fuels, exhibit significant corrosion resistance and, compared to heat-resistant steels, also have higher creep resistance.
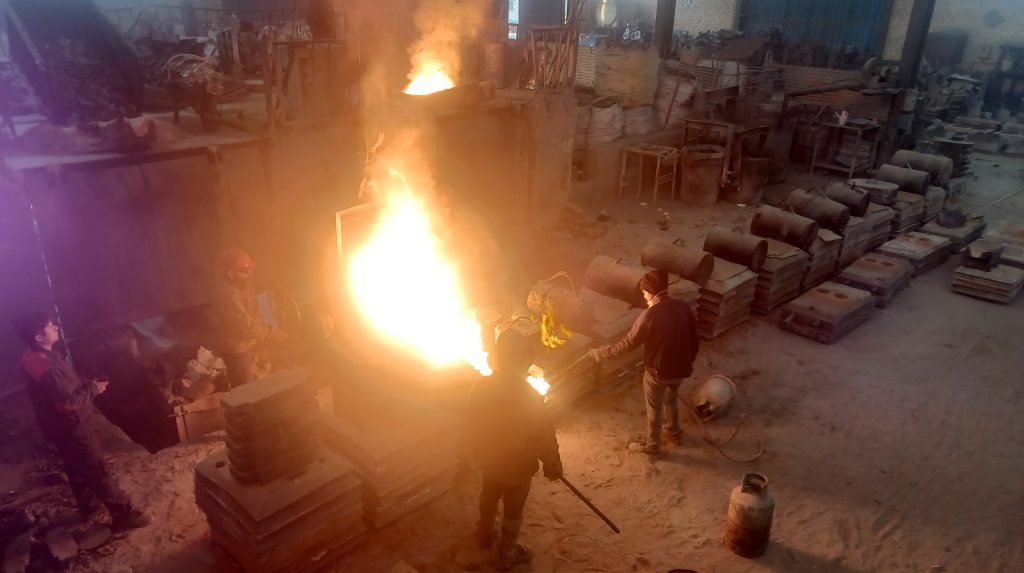
The melting point and boiling point are unique and specific to each element. If two metals are combined to form an alloy, their melting and boiling points change. Knowing the melting points of elements and alloys helps industrialists melt them in a principled and standardized manner, ensuring no issues arise for the metal or alloy in question. Iron and steel also have specific melting points, and enthusiasts and professionals in this field must not only know the melting point of iron and steel but also the melting points of all alloys related to these two metals. Here, we intend to discuss and examine the melting point of iron, steel, and their various alloys.
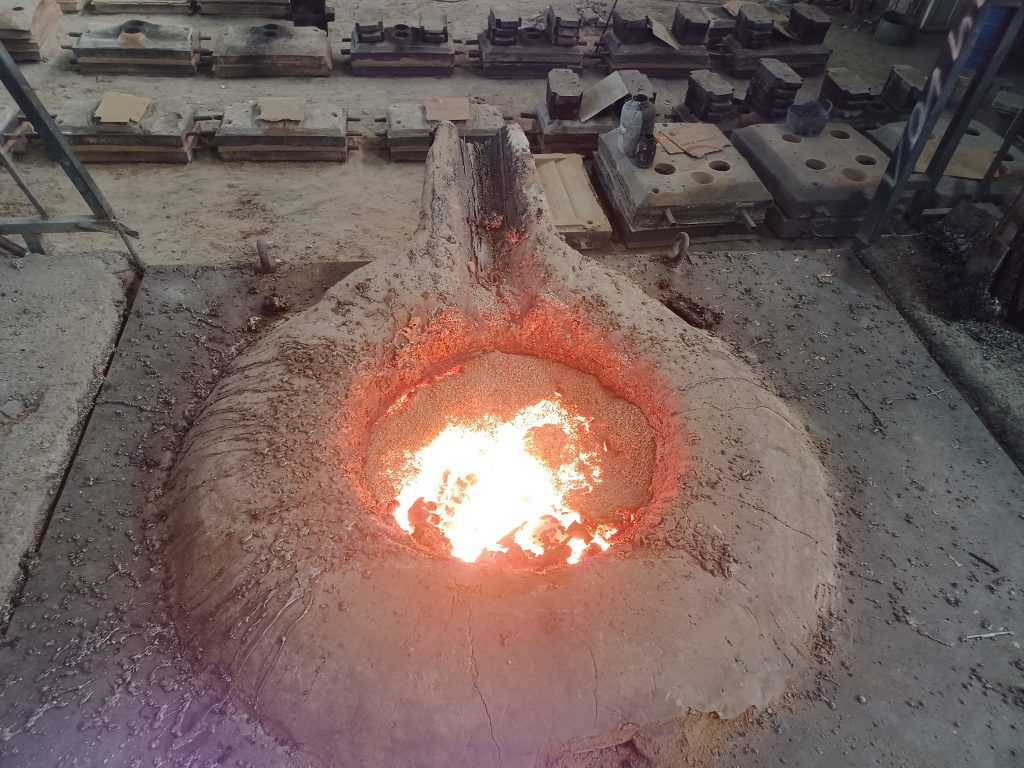
Melting Point of Iron
The atoms in solids are arranged in a specific order and pattern. In fact, heating a metal or element causes vibrations within it. This applied temperature causes the atoms of the element to move, giving the element malleability and flexibility.
Pasty Melting: Since alloys have their own phase diagrams, and their melting to solidification temperatures are defined according to these diagrams, by selecting the pasty temperature and heating iron, the material reaches a state that is a mixture of solid and liquid.
Melting Point of Sponge Iron
Sponge iron is obtained by removing oxygen gas from iron ore using reducing agents and carbon. During the conversion of iron to steel, one of the steps required is the conversion of iron ore to sponge iron. The melting point of sponge iron is around below 1200°C. This low melting point is due to the presence of about 30 to 35% impurities.
Melting Point of Pure Iron
The iron commonly used is iron with some impurities. Pure iron has a different melting point compared to impure iron. The melting point of iron can vary depending on the size and chemical composition of the impurities, and it can be higher or lower than the standard point. Iron, as a material obtained from iron ore, has a specific melting point. The melting point of pure iron is standardly 1538°C.
Melting Point of Steel
Steel is an alloy of iron. Pure iron, which we discussed earlier, is very soft and corrosive, and because it reacts with oxides and sulfides in the environment, it cannot be used in active environments. One of the results of adding carbon to iron is that it reduces reactivity and eliminates this drawback of pure iron. The melting point of steel is approximately 1425-1540°C.
Melting Point of CK45 Steel
CK45 steel, due to its good mechanical and physical properties, has wear and impact resistance, but unfortunately, due to the low chromium content, this steel is not resistant to rust and corrosion. The melting point of this steel depends on the amount and percentage of its constituent materials. However, on average, the melting point of this type of steel is considered to be between 1514-1560°C.
Melting Point of Stainless Steel
Stainless steel, due to its high resistance to corrosion, is one of the types of steel widely used in materials engineering. The presence of approximately 12% chromium in the composition of stainless steel gives it high resistance. By producing stainless steel and adding it to iron, the iron surfaces are protected from oxidation and corrosion. Some types of stainless steel also contain nickel, molybdenum, tungsten, niobium, titanium, vanadium, and aluminum, which increase their corrosion resistance and, consequently, raise the cost of producing stainless steel castings. Stainless steel includes various grades, and since it is considered an alloy, different grades have different melting points. Additional alloys also pass through the melting range of the element. Pure iron (Fe) has a fixed melting point of 1538°C, chromium (Cr) 1860°C, and nickel (Ni) 1453°C, compared to a wide range of 1400-1530°C for stainless steel.
- It is worth mentioning that Avangard Company has successful experience in producing stainless steel or stainless steel (Stainless Steel) in the following types:
- Austenitic Stainless Steel (200 series and 300 series)
- Ferritic Stainless Steel
- Martensitic Stainless Steel
- Duplex Stainless Steel
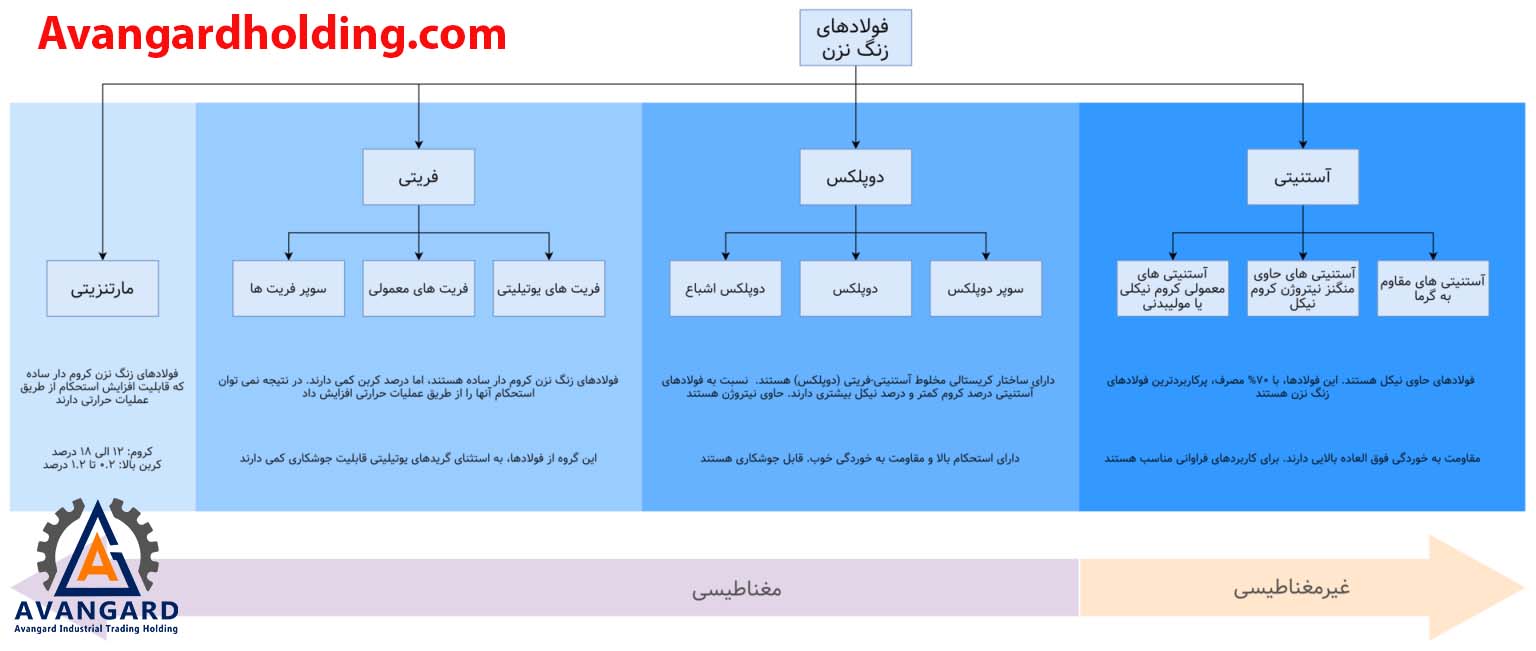
Melting Point of 316 Steel
Steel refers to an alloy whose base is the element iron and contains less than 2% carbon. 316 steel contains a combination of nickel, chromium, and molybdenum. The presence of molybdenum in the composition of this material is to enhance the steel’s resistance to chloride-induced corrosion. If the letter “L” appears after the name of this steel, it indicates a low carbon content used in the alloy, and this low amount of carbon ensures that the protective layer remains intact even after welding. One of the primary methods of producing this type of 316 steel is recycling its scrap, and about 70% of the produced steel is formed by melting the scrap of this steel and recasting it. 316 steel is a subset of stainless steel, and its melting point is approximately the same as that of stainless steel. It is worth mentioning that Avangard Company has an outstanding track record in producing 316L steel components.
Cast iron, like steel, is an alloy composed of iron and carbon. However, there is a major difference: the carbon content in cast iron is above 2%, while the carbon content in steel is up to approximately 2.1%. Cast iron falls under the category of casting alloys. In steel, other elements such as silicon, manganese, nickel, and chromium are also present. Casting cast iron is much easier, and it has less shrinkage compared to steel. This property makes cast iron a more ideal metal than steel for ornamental iron structures and architecture. Cast iron is more vulnerable to corrosion than steel and also has lower toughness, is less bendable, and is more brittle. The production cost of steel is higher than that of cast iron. However, if we intend to compare the melting points of these two materials, although both are alloys of iron, cast iron has a lower melting point than steel. The melting point of cast iron is approximately 950 to 980°C.
Chemical compositions and metallurgical structure are two very important factors in the melting point of steel. While the melting point of iron is a fixed number, there are certain actions that can vary this number, raising or lowering the melting point. However, the effect of chemical compositions is greater than that of the metallurgical structure and may alter the melting point of steel. Based on the above, it can be concluded that as the impurities in iron increase, the melting point also increases, and the higher the percentage of carbon in the alloy, the lower its melting point compared to pure iron. This factor affects the price of castings as a steel product.
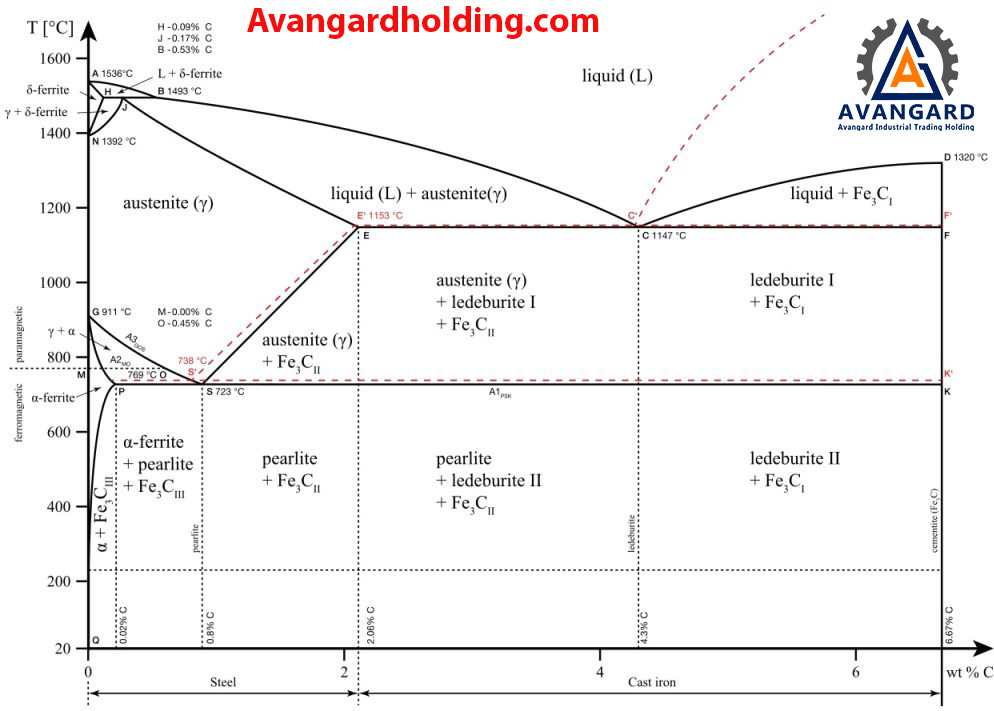
With the advancement of technology and the development of science, the melting point has become increasingly important and is more widely used in industry.
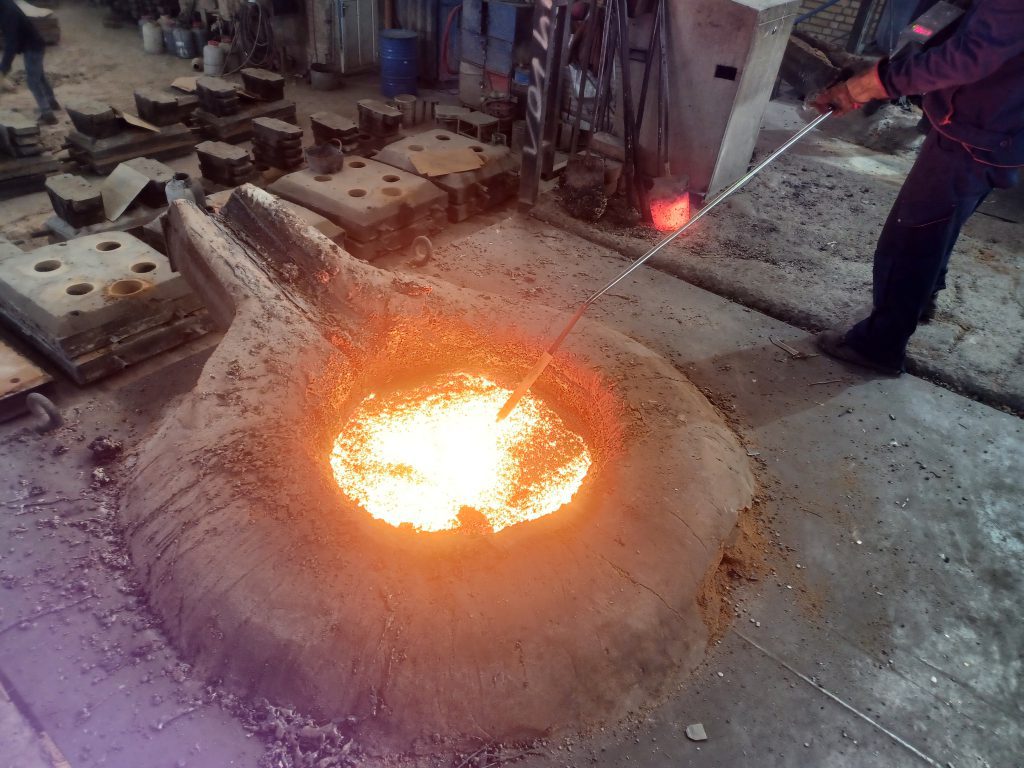
Understanding the melting temperature of molten metal is crucial and vital for a foundry worker. Not knowing the melting temperature of the desired alloy and overheating it can lead to numerous issues, such as reducing the lifespan of the furnace and ladle linings, wasting and burning some beneficial elements in the melt, phase and nature changes in the melt, burning and deformation of the mold after pouring, gas absorption in some materials, and other problems. Conversely, not knowing that the molten temperature is too low and proceeding with casting can cause issues such as slag formation in the pouring ladle or mold channels, incomplete filling of the mold, failure to achieve the desired properties, and more.
Therefore, knowing the correct molten temperature is one of the most important pieces of information for a foundry worker. For some alloys, knowing the exact melting temperature is as critical as knowing the chemical composition of the alloying elements.
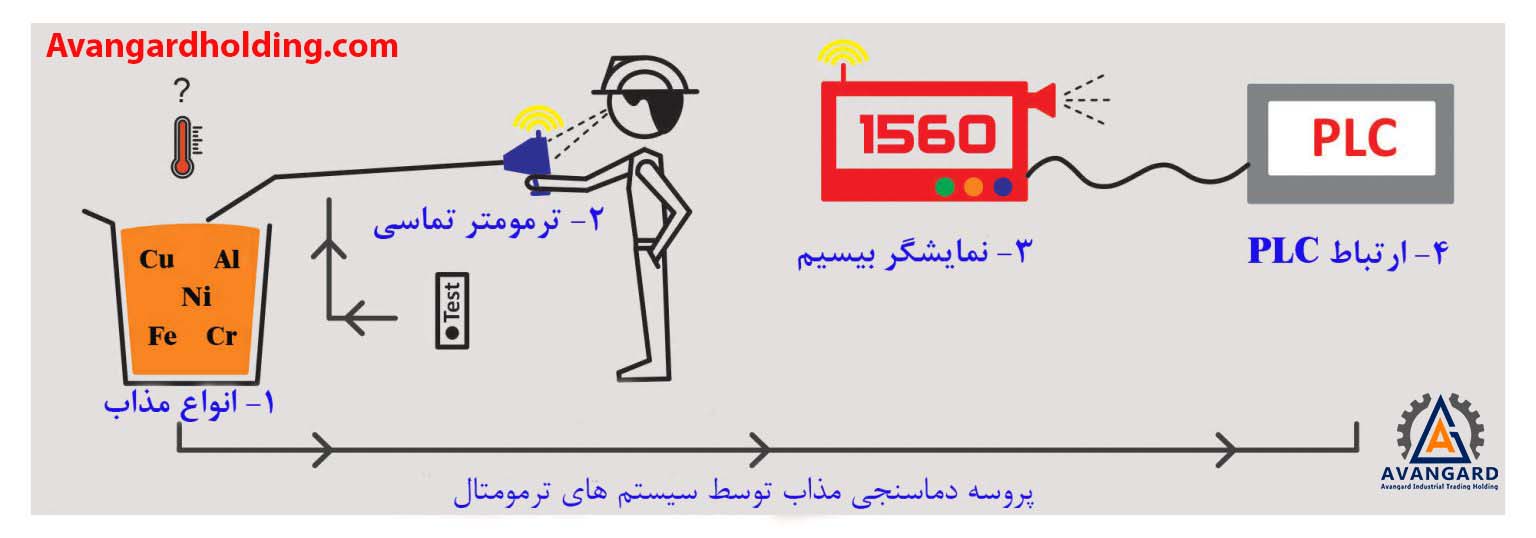
1- Specialized casting of various wear-resistant steels and cast irons, such as manganese steels (Hadfield) with different percentages of manganese and molybdenum, Ni-Hard cast iron, and high-chromium cast irons used as hammers, anvils, and liners in sand, cement, and aggregate crushers, offered at competitive prices and high quality.
*It is worth reiterating that Avangard Company, with its experienced engineering team, has extensive expertise in producing a wide range of alloys. The complete list of crusher machine parts is available in the products section and will be provided to you at the best price and highest quality.
2- Casting of various carbon and low-alloy steels, including alloys from the GS… group, WCB, 42CrMo4 (Mo40), Gs – Ck45, surface-hardening steels such as 1.7131, and other cast alloys in this group of steels.
*The above steels are used in machinery manufacturing, railway industries, and oil and gas industries.
3- Casting of various stainless steels (Stainless steel), such as 304, 316, 316L, Ni-Resist cast iron, and special alloys like Duplex steel.
*In this field, the company has experience in producing various impellers and pump bodies for water, oil, gas, salt, or acid transportation. Alloys containing Ti, Nb, N, V, and W have been frequently produced and delivered to customers.
4- Casting of various heat-resistant steels, such as alloys 1.4841, 1.4848, 1.4837, 1.4823, and others, used in high-temperature environments in cement, oil and gas, and petrochemical industries.
5- Casting of various gray cast irons (GG) and ductile cast irons (GGG) in accordance with international standards such as DIN, ASTM, BS, and others.