Heat treatment refers to a process in which metals, in their solid state and without changing their external shape, are heated to a specific temperature under controlled conditions and then cooled to achieve desirable and excellent properties. Almost all metals can undergo heat treatment, and their reactions to this process vary. Heat treatment is one of the reasons for the widespread production and application of steel in the industry. The temperature at which steels are subjected to various heat treatments is above 723 degrees Celsius.
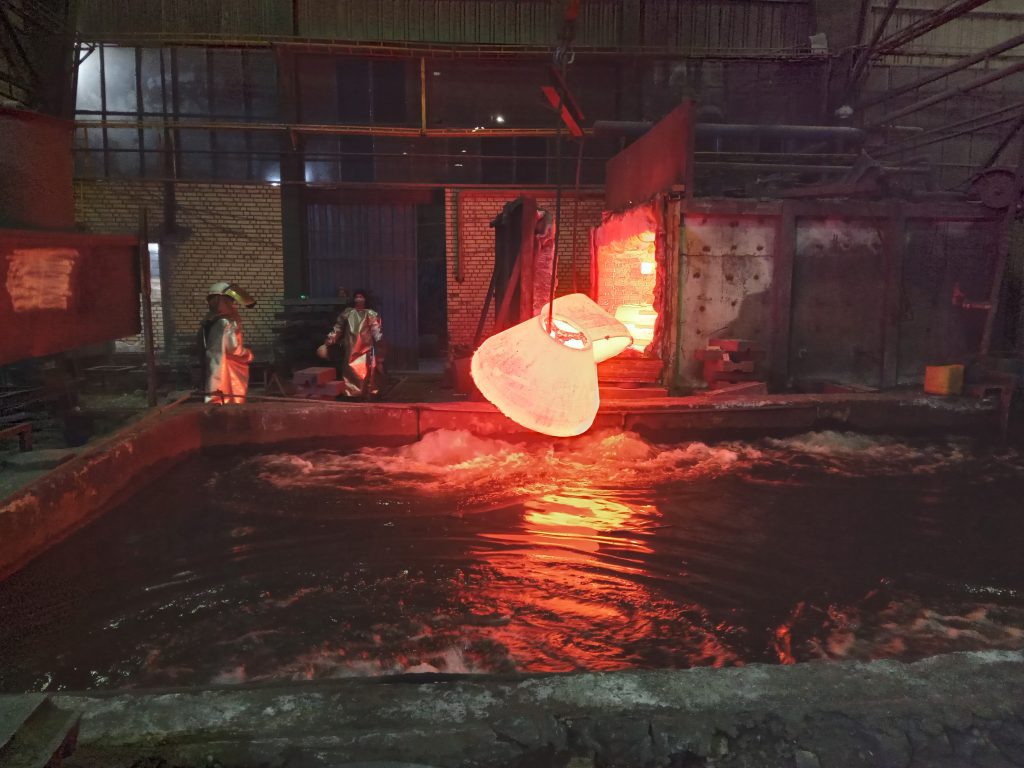
Given the importance of the heat treatment stage in the final properties of the part, this phase holds special significance at Avangard Company. All heat treatment cycles are carefully tested, selected, and executed. Then, the appropriate furnace with various capacities and dimensions is used based on the dimensions and heat treatment cycle of the parts. Additionally, using a sophisticated computer system, the accuracy of the heat treatment cycle and the uniformity of the furnace temperature are monitored and recorded.
In this unit, various heat treatment services such as hardening, annealing, normalizing, and stress relieving are performed on the produced parts as needed.
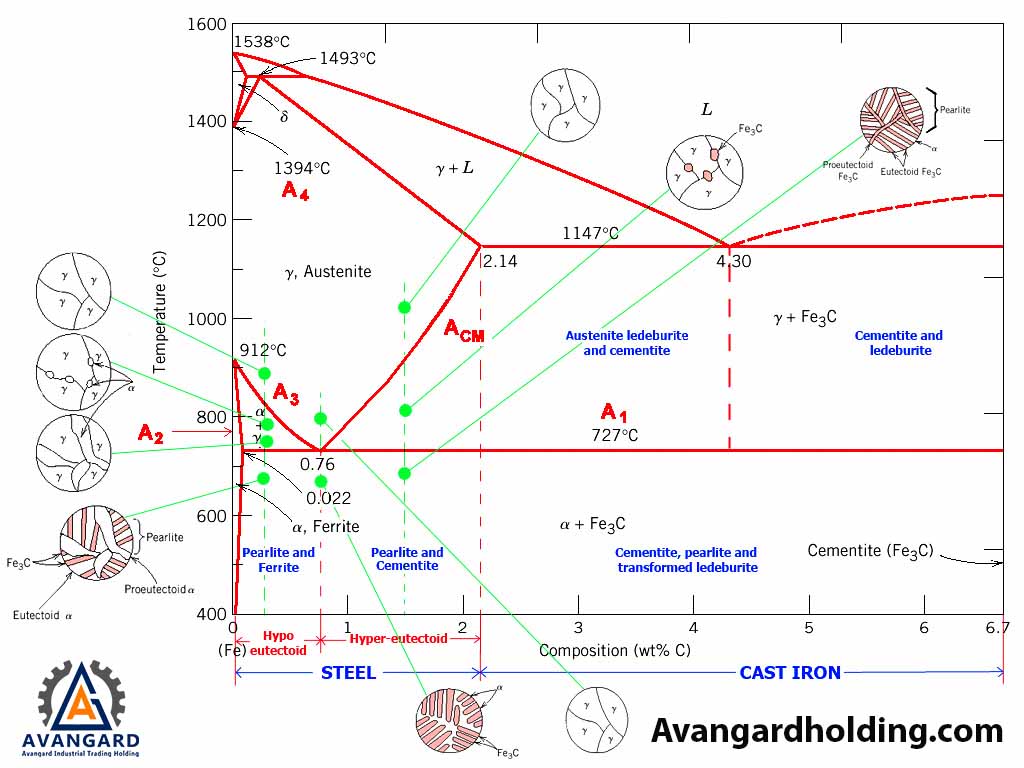
To harden medium or high-carbon steels, the part is first heated above a critical temperature (around 760 degrees Celsius) and allowed to remain at that temperature for a period to achieve equilibrium. Then, it is rapidly immersed in a bath of oil or water to cool it to room temperature. This sudden cooling results in the formation of a supersaturated solution called “martensite,” which is very hard. However, this phase is also very brittle. In fact, as the hardness of the part increases, its toughness decreases.
After the quenching process, the part can be reheated to a lower temperature (around 200 to 700 degrees Celsius), heat-soaked, and then slowly cooled. The tempering heat treatment process causes a portion of the martensite to transform back into ferrite and cementite. This reduces hardness but partially restores the ductility or malleability of the part. By varying the time and temperature parameters in this process, different types of steels with varying properties can be produced. With over two decades of experience, Avangard Engineering Company can produce the required steel for various applications using this method.
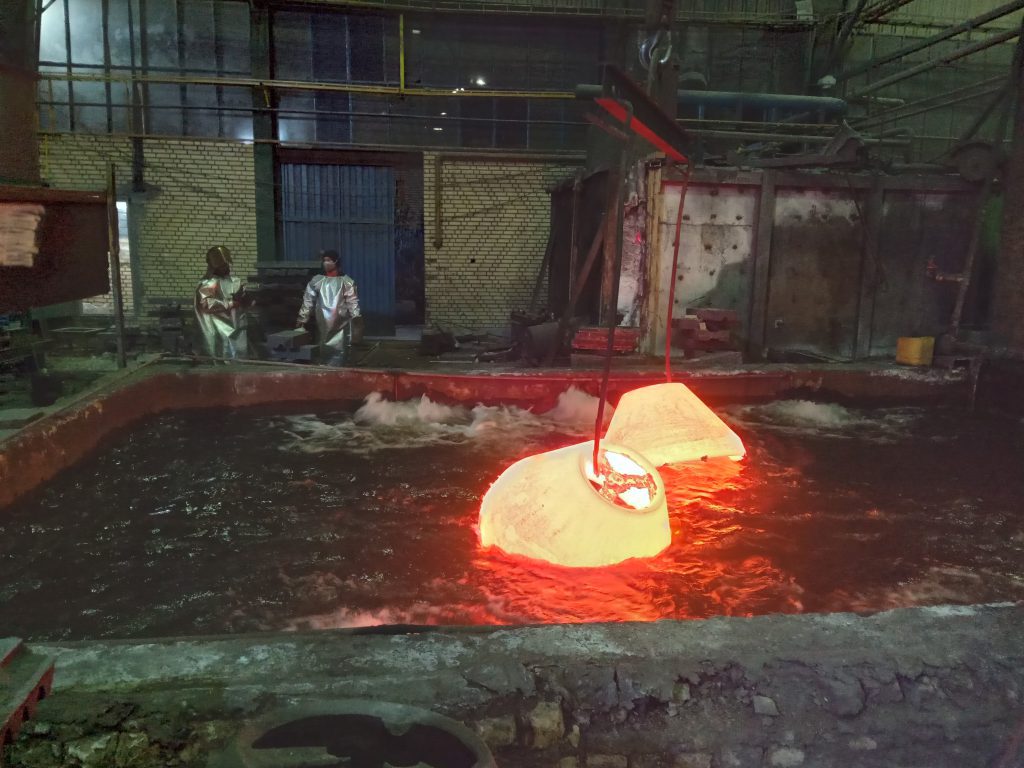
Annealing is a heat treatment process used to soften (reduce hardness), homogenize the structure, and relieve residual stresses in a material. Generally, any heat treatment process that results in a structure with lower hardness and higher ductility compared to the martensitic structure is considered annealing. The annealing heat treatment is divided into more specific and precise processes, which vary based on the cooling method, final structure and properties, and the temperature of the process.
In metallurgy, annealing is a heat treatment that alters the physical properties of materials to increase their ductility, reduce hardness, and optimize their suitability for cold working. During the annealing process, atoms in the crystalline structure are rearranged, and the number of dislocations is reduced, leading to changes in toughness and hardness.
Annealing is not only applied to steels but also to other alloys such as aluminum, copper, and brass. In general, annealing is beneficial in any case where a brittle part needs to undergo deformation at low temperatures. Phenomena such as recrystallization and the growth of stress-free equiaxed grains are among the side effects of the annealing process.
The solution annealing process is typically used to improve the properties of stainless steels and nickel alloys, with a focus on enhancing corrosion and heat resistance. However, its primary application is in austenitic stainless steels. The main goal of solution annealing is to eliminate precipitates in the microstructure, which improves corrosion and heat resistance.
In the solution annealing process, the part is heated to a temperature where a single-phase structure is achieved. It is then rapidly quenched in water or air to room temperature to prevent the formation of carbide precipitates during the fastest cooling phase.
The single-phase structure after solution annealing is highly significant. Subsequently, processes such as precipitation hardening or aging may also be performed. The goal of these processes is to create precipitates with specific characteristics, ensuring that only the desired precipitates are present in the final product. The composition, size, and quantity of these precipitates formed during aging determine the final hardness, strength, and other mechanical properties of the product.

In general, the normalizing process is primarily used to alter the mechanical properties of metals. The part is heated to a temperature within the austenite range and then cooled in open air to room temperature. The austenitizing temperature is approximately 55 degrees Celsius above the critical line Ac3 for hypoeutectoid steels and 50 degrees Celsius above the critical line Acm for hypereutectoid steels. This process involves heating the part to the austenite phase stability temperature and then cooling it in open air, aiming to achieve a structure with fine, equiaxed grains and suitable mechanical and machining properties.
Normalizing is performed to uniformly distribute alloying elements, refine the grain structure that has coarsened during hot working or casting, dissolve precipitated carbides, and break down the continuous carbide network that has formed at grain boundaries during previous processes.
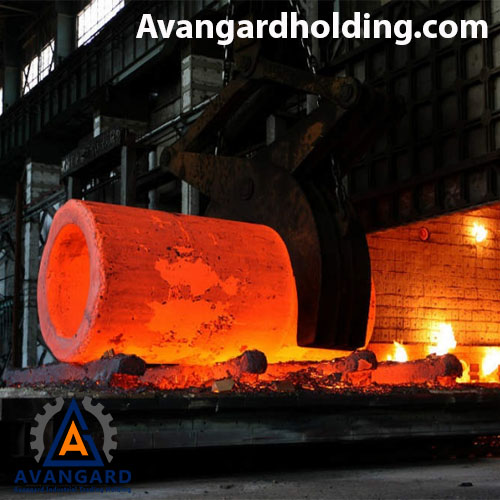
To minimize residual stresses in the part, stress relieving is performed after casting. Stress relieving reduces the risk of cracking, warping, and dimensional changes during service or subsequent operations.
Some heat treatment or mechanical processes in parts can cause the formation of internal stresses, which can be destructive and adversely affect the performance of these parts. The resulting internal stresses can lead to cracking, warping, or failure of the parts at stress levels much lower than their designed stress limits. Sources of internal stresses include:
1- Non-uniform cooling of different areas of the part during cooling from the austenite region.
2- Machining and cold working.
3- Welding.
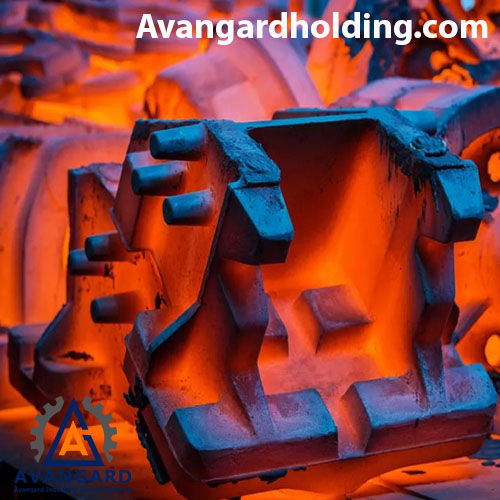
To eliminate residual stresses, the parts in question are heated to a temperature below the critical temperature Ac1 for a specified period. The heating time depends on the dimensions of the part and the stress-relieving temperature. To prevent the creation of new thermal stresses and the risk of cracking or warping, heating to the stress-relieving temperature and cooling from that temperature are performed very slowly and in accordance with standards. During stress relieving, no significant changes occur in the mechanical properties of the part, as the process only involves the removal of stresses through recovery heat treatment.